What are the common surface treatment methods? What are the applicable surface treatment methods for various materials?
Release time:
2022-04-06
Source:
Xinmin.com
I. Surface mechanical strengthening
Mechanical treatment methods are often used in industry to clean, strengthen and brighten the metal surface, such as shot peening, tumbling, bore extrusion and grinding and polishing, etc., of which shot peening, polishing treatment is widely used in the production.
(A) Shot blasting
Shot blasting is the use of high-speed jet of sand or iron shot, the surface of the workpiece for a strong impact, so that the surface plastic deformation, so as to strengthen the surface and change the surface state of a process method. The method of shot blasting usually has two kinds of manual operation and mechanical operation. Commonly used shot blasting are the following: cast iron shot, steel shot, glass shot, sand shot, etc., of which ferrous metals are often used cast iron shot, steel shot and glass shot, while non-ferrous metals and stainless steel commonly used glass shot and stainless steel shot.
Shot peening is a surface peening process widely used in factories, its equipment is simple, low cost, not limited by the shape and location of the workpiece, easy to operate, but the working environment is poor. Shot blasting is widely used to improve the mechanical strength of parts as well as wear resistance, fatigue resistance and corrosion resistance. Can also be used for surface matting, oxide skin removal and elimination of castings, forging, welding parts of residual stress.
(B) polishing and polishing
Polishing polishing is the use of polishing wheels on the surface of the parts to obtain a flat and smooth grinding surface of a surface treatment method. Its role is to remove the surface of the parts of rust, sand eyes, welding slag, scratches and other defects, to improve the surface flatness of the parts. Grinding is divided into two types of coarse grinding and fine grinding. Rough grinding is the rough surface and irregular shape correction shape, available manually or mechanically. Most of the manual operations are used for non-ferrous metals; mechanical operations are used for steel, generally on the grinding wheel; after rough grinding the metal surface abrasion marks are very deep and need to be eliminated by fine grinding, in preparation for polishing. Fine grinding has manual fine grinding and mechanical fine grinding. Manual fine grinding is from coarse to fine in each number of metallographic grinding wheel; mechanical fine grinding commonly used pre-grinding, wax disc, polishing paste to accelerate the fine grinding process. Grinding with abrasive, for bronze, brass, cast iron, zinc and other soft materials with artificial emery; for steel with artificial corundum. Diamond can be used for all metal polishing, especially for soft and tough metal materials.
Polishing polishing is the final process of decorative processing of the plated surface or parts surface, its purpose is to eliminate the grinding process after the residual on the surface of the fine abrasive marks, to obtain a bright appearance. Polishing methods are mechanical, chemical, electrolytic, etc., the commonly used method is polishing wheel polishing, it is several layers of circular cloth, fleece, blankets, etc. sewn into a wheel-shaped, installed in the polishing machine shaft to make it rotate polishing. Polishing wheel carrier many kinds of cotton, hemp, wool, paper, leather, plastic and its mixture, etc.; abrasive material particles fine and uniform, polygonal shape, sharp edge. Commonly used polishing powder types, properties, uses as shown in Table 2-1. Coarse polishing with a binder to stick the abrasive powder on the polishing wheel, available diamond, iron oxide abrasive powder, also available chromium oxide abrasive powder, or the use of semi-solid or liquid abrasive.
Second, conversion film processing
Transformation film treatment is to immerse the workpiece in certain solutions, under certain conditions to produce a dense protective film on its surface, to improve the ability of the workpiece to prevent corrosion and increase the decorative effect. Commonly used conversion film treatment are oxidation treatment and phosphate treatment.
(A) oxidation treatment
Steel oxidation treatment steel oxidation treatment is the steel parts in the air - water vapor or chemical drugs heated to the appropriate temperature, so that its surface to form a blue (or black) oxide film to improve the corrosion resistance of steel and appearance, this process is called oxidation treatment, also known as blue treatment. The oxide film is a dense and solid Fe3O4 film, only 0.5 ~ 1.5mm thick, no effect on the dimensional accuracy of the steel parts. After the oxidation treatment, the steel parts are also subjected to soap solution impregnation treatment and oil immersion treatment to improve the anti-corrosion ability and lubrication performance of the oxide film. Steel oxidation treatment has the following basic process: the higher the oxidant content in the solution during oxidation treatment, the faster the generation of oxide film, and the film layer is dense and solid. The concentration of alkali in the solution is increased appropriately to obtain an increase in the thickness of the oxide film, and the alkali content is too low to obtain a thin and fragile oxide film. The temperature of the solution should be increased to improve the oxidation density. The higher the carbon content of the workpiece, the easier the oxidation and the shorter the oxidation time. Oxidation treatment time is mainly adjusted according to the carbon content of the steel and the oxidation requirements of the workpiece. Oxidation treatment process does not affect the accuracy of the parts, commonly used in instruments, meters, tools, firearms and certain mechanical parts of the surface, so that it achieves wear resistance, corrosion resistance and protection and decoration purposes.
Oxidation treatment of aluminum and its alloys Aluminum (or aluminum alloy) can easily produce dense oxide film under natural conditions, which can prevent the oxidation and erosion of moisture and harmful gases in the air, but it is easy to be corroded in alkaline and acidic solutions. In order to obtain a better protective oxide film on the surface of aluminum and aluminum alloys, an oxidation treatment should be applied. The commonly used treatment methods are chemical oxidation and electrochemical oxidation. Chemical oxidation method is to put the aluminum (or aluminum alloy) parts into the chemical solution for oxidation treatment to obtain a solid oxide film, the thickness of 0.3 ~ 4 mm. according to the nature of the treatment solution can be divided into alkaline and acidic solution oxidation treatment. For example, the alkaline oxidation solution is Na2CO3 (50 g/L), Na2CrO4 (15 g/L), NaOH (25 g/L), processing temperature: 80-100°C, processing time: 10-20min. after the oxidation treatment, the aluminum surface shows a thickness of 0.5-1mm golden oxide film. This method is suitable for pure aluminum, aluminum-magnesium, aluminum-manganese alloy. Chemical oxidation method is mainly used to improve the corrosion resistance and wear resistance of aluminum and aluminum alloy, and this process method is easy to operate, low cost, and suitable for mass production. Electrochemical oxidation method is a method to form an oxide film on the surface of aluminum and aluminum alloy in electrolytic solution, also called anodic oxidation method, in which the workpiece with aluminum (or aluminum alloy) as the anode is placed in the electrolytic solution and oxygen is generated on the anode after being energized, which causes chemical or electrochemical dissolution of aluminum or aluminum alloy, resulting in the formation of an oxide film on the surface of the anode. The anodic oxide film not only has good mechanical and corrosion resistance properties, but also has strong adsorption properties, and after using different coloring methods, it can also obtain a variety of different colors of decorative appearance. In order to obtain different nature of oxide film on the surface of aluminum and aluminum alloy, different kinds of electrolytes are often used to achieve. The commonly used electrolytes are sulfuric acid, chromic acid and oxalic acid, etc. The basic process of aluminum and aluminum alloy oxidation treatment is as follows: Due to the porous structure and strong adsorption property of the anodic oxide film, the surface is easy to be contaminated, especially the corrosive medium is easy to cause corrosion when it enters the pore. Therefore, after the anodic oxide film is formed, it must be closed to close the pores of the oxide film to improve the corrosion resistance, insulation and wear resistance, and to weaken the adsorption of impurities or oil. Commonly used sealing methods are steam sealing method and paraffin, oil, resin sealing method.
(B) phosphate treatment
The steel parts immersed in a phosphate-based solution so that its surface deposition, the formation of water-insoluble crystalline phosphate conversion film process known as phosphate treatment. Commonly used phosphate treatment solution for manganese iron phosphate salt and zinc phosphate solution, phosphate treatment after the phosphate film thickness is generally 5 to 15 mm, its corrosion resistance is 2 to 10 times the bluing treatment. Phosphate film and the substrate bonding force is strong, with good corrosion protection and high insulation properties, in the atmosphere, oil, benzene and toluene and other media have good corrosion resistance, oil, wax, pigments and lacquer, etc. have excellent absorption, suitable for paint primer. However, the strength of the phosphate film itself, the hardness is low, there is a certain brittleness, when the steel deformation is larger, easy to appear fine cracks, not resistant to impact, in acid, alkali, seawater and water vapor corrosion resistance is poor. After the phosphate treatment for surface dipping paint, oil dipping treatment, corrosion resistance can be greater. Phosphate treatment requires simple equipment, easy to operate, low cost, high production efficiency. In general mechanical equipment can be used as a protective layer of steel material parts, but also as a variety of weapons lubrication layer and protective layer.
(C) electroplating and chemical plating
Electroplating is the plating of metal products as a cathode, the application of direct current, so that the cations of metal salt solution deposited on the surface of the workpiece to form a plating layer. Plating is essentially an electrolytic process in which the weight of the material precipitated on the cathode is proportional to the current strength and time. The three conditions necessary to perform electroplating are: power supply, bath (degree solution) and electrodes. Electroplating can cover the material or part with a layer of relatively uniform and well-bonded coating to change its surface characteristics and appearance for material protection or decoration purposes. In addition to making the product beautiful and durable, electroplating can also obtain special features that can improve the corrosion resistance, wear resistance, heat resistance, reflectivity, electrical conductivity, lubricity, surface hardness of metal products and repair the size of worn parts and surface defects, such as gold plating on semiconductor devices, can obtain very low contact resistance; aluminum-tin alloy plating on electronic components can obtain very Good brazing performance; in the piston ring and shaft chromium plating can obtain high wear resistance; prevent local carburization of copper plating, prevent local nitriding of tin plating, etc.. At present, the widely used plating processes are copper plating, nickel plating, chromium plating, zinc plating, silver plating, gold plating, etc.
Chemical plating is also known as electroplating without external power supply. The principle is: metal deposition in aqueous solution generally proceeds according to the following formula: M2+ + 2e → M, i.e., there are two positively charged metal ions M in the solution, when it receives two electrons, it is transformed into metal atoms M, which are deposited on the surface of the workpiece under appropriate conditions to form a coating. Chemical plating obtains electrons by chemical reaction directly in the solution, and it generally has several kinds of charge exchange deposition, contact deposition, reduction deposition, etc. At present, chemical nickel, copper, silver, gold, cobalt, palladium, platinum and tin plating have been applied in industrial production, especially in the electronics industry.
General knowledge of surface treatment applications
For detailed tables, please visit: http://www.josen.net/Steel-Knowledge/1602812850.html page to view.
Stainless steel surface treatment
Stainless steel has a unique strength, high wear resistance, superior corrosion resistance and not easy to rust and other excellent characteristics. Therefore, it is widely used in the chemical industry, food machinery, electromechanical industry, environmental protection industry, household appliances industry and home decoration, finishing industry, giving people a gorgeous and noble feeling.
Stainless steel application development prospects will become more and more extensive, but the development of stainless steel applications largely determine its surface treatment technology development degree.
1 Stainless steel common surface treatment methods
1.1 Stainless steel varieties introduction
1.1.1 Stainless steel main components: generally contains chromium (Cr), nickel (Ni), molybdenum (Mo), titanium (Ti) and other high-quality metal elements.
1.1.2 Common stainless steel: there are chromium stainless steel, containing Cr ≥ 12% or more; nickel-chromium stainless steel, containing Cr ≥ 18%, containing Ni ≥ 12%.
1.1.3 Classification from stainless steel metallographic organization: there are austenitic stainless steel, for example: 1Cr18Ni9Ti, 1Cr18Ni11Nb, Cr18Mn8Ni5. martensitic stainless steel, for example: Cr17, Cr28, etc.. Generally known as non-magnetic stainless steel and with magnetic stainless steel.
1.2 Common stainless steel surface treatment methods
Commonly used stainless steel surface treatment technology has the following treatment methods: ① surface natural whitening treatment; ② surface mirror bright treatment; ③ surface coloring treatment.
1.2.1 Surface natural whitening treatment: stainless steel in the processing process, after the rolled plate, tied edge, welding or after artificial surface fire baking heating treatment, resulting in black oxide skin. This hard gray-black oxide skin is mainly NiCr2O4 and NiF two EO4 components, the previous general use of hydrofluoric acid and nitric acid for strong corrosion methods to remove. However, this method is costly, polluted environment, harmful to human body and corrosive, gradually eliminated. At present, there are two main treatment methods for oxide skin.
(1) sandblasting (pill) method: mainly using the method of spraying micro-glass beads to remove the surface of the black oxide skin.
(2) chemical method: the use of a non-polluting pickling passivation paste and room temperature non-toxic cleaning solution with inorganic additives for dipping. Thus achieving the purpose of whitening treatment of stainless steel natural color. After the treatment basically looks like a color of no light. This method is more suitable for large, complex products.
1.2.2 Stainless steel surface mirror bright treatment method: according to the complexity of stainless steel products and user requirements of different situations can be used respectively mechanical polishing, chemical polishing, electrochemical polishing and other methods to achieve a mirror luster. The advantages and disadvantages of these three methods are as follows.
1.2.3 Surface coloring treatment: stainless steel coloring not only gives stainless steel products a variety of colors, increasing the variety of products, but also to improve the wear resistance and corrosion resistance of the product.
Stainless steel coloring methods are as follows.
(1) chemical oxidation coloring method.
(2) electrochemical oxidation coloring method.
(3) ion deposition oxide coloring method.
(4) high-temperature oxidation coloring method.
(5) gas phase cracking coloring method.
A brief overview of the various methods is as follows.
(1) Chemical oxidation coloring method: It is the color of the film formed by chemical oxidation in a specific solution, and there are dichromate method, mixed sodium salt method, sulfide method, acidic oxidation method and alkaline oxidation method. Generally "INCO method" (INCO) is used more often, but to ensure a batch of products with the same color, you must use reference electrodes to control.
(2) Electrochemical coloring method: The color of the film is formed by electrochemical oxidation in a specific solution.
(3) ion deposition oxide coloring method chemical method: is the stainless steel workpiece in the vacuum coating machine for vacuum evaporation plating. For example: titanium-plated watch cases, watch bands, generally golden yellow. This method is suitable for high-volume product processing. Because of the large investment, high cost, small batch products are not cost-effective.
(4) high-temperature oxidation coloring method: is in a specific molten salt, immersed in the workpiece to maintain a certain process parameters, so that the workpiece to form a certain thickness of oxide film, while showing a variety of different colors.
(5) gas phase cracking coloring method: more complex, less used in industry.
1.3 Treatment method selection
Stainless steel surface treatment selection of which method, according to the product structure, material, and different requirements for the surface, choose the appropriate method for processing.
2 common causes of rust corrosion of stainless steel parts
2.1 Chemical corrosion
2.1.1 surface pollution: attached to the surface of the workpiece oil, dust and acid, alkali, salt, etc. in certain conditions into a corrosive medium, and some components of the stainless steel parts in a chemical reaction, resulting in chemical corrosion and rust.
2.1.2 Surface scratches: various scratches on the damage to the passivation film, so that the stainless steel protection capacity is reduced, easy to react with chemical media, chemical corrosion and rust.
2.1.3 Cleaning: pickling passivation after cleaning is not clean, resulting in residual liquid retention, direct corrosion of stainless steel parts (chemical corrosion).
2.2 Electrochemical corrosion
2.2.1 carbon steel pollution: contact with carbon steel parts caused by scratching and corrosion media to form primary cells and electrochemical corrosion.
2.2.2 cutting: cutting slag, splash and other rust-prone material adherence and corrosion media to form primary cells and electrochemical corrosion.
2.2.3 Baking school: flame heating area composition and metallurgical organization changes and uneven, and corrosion media to form a primary cell and electrochemical corrosion.
2.2.4 welding: physical defects in the welding area (edge biting, porosity, cracks, not fused, not welded through, etc.) and chemical defects (coarse grains, grain boundary poor chromium, segregation, etc.) and corrosion media to form a primary cell and electrochemical corrosion.
2.2.5 Material: The chemical defects of stainless steel (uneven composition, S, P impurities, etc.) and surface physical defects (porosity, sand holes, cracks, etc.) are conducive to forming galvanic cells with corrosive medium and producing electrochemical corrosion.
2.2.6 Passivation: Poor pickling passivation effect causes uneven or thin passivation film on stainless steel surface, which is easy to form electrochemical corrosion.
2.2.7 Cleaning: The residual pickling passivation liquid and the products of chemical corrosion of stainless steel will form electrochemical corrosion with stainless steel parts.
2.3 Stress concentration tends to cause stress corrosion
In short, stainless steel because of its special metallographic structure and surface passivation film, so that it is difficult to react with the medium in general and be corroded, but not under any conditions can not be corroded. In the corrosive medium and inducement (such as scratch, splash, slag cutting, etc.) under the condition of existence, stainless steel can also occur slow chemical and electrochemical reaction corrosion with corrosive medium, and under certain conditions the corrosion rate is quite fast and corrosion phenomenon, especially pitting corrosion and crevice corrosion. The corrosion mechanism of stainless steel is mainly electrochemical corrosion.
Therefore, in stainless steel products in the process of processing operations should take all effective measures to avoid corrosion conditions and incentives. In fact, many corrosion conditions and inducements (such as scratches, spatter, slag cutting, etc.) also have significant adverse effects on the appearance quality of products, and should and must be overcome.
3. There are problems in the processing of stainless steel products
3.1 Defects of welding seams: serious defects of welding seams are remedied by manual and mechanical grinding, resulting in uneven surface and affecting appearance.
3.2 Surface inconsistency: only pickling passivation of the weld will cause uneven surface and affect the appearance.
3.3 Scratches are difficult to remove: the overall pickling passivation, also can not remove all kinds of scratches produced in the process of processing, and also can not remove due to scratches, welding splash and adhesion to the surface of stainless steel carbon steel, splash and other impurities, resulting in the presence of corrosion medium under the condition of biochemical corrosion or electrochemical corrosion and rust.
3.4 Uneven polishing passivation: pickling passivation treatment after manual polishing, for large area of the workpiece, it is difficult to achieve uniform treatment effect, can not get an ideal uniform surface. In addition, the cost of working hours and auxiliary materials is also higher.
3.5 Limited pickling ability: pickling passivation paste is not omnipotent, for plasma cutting, flame cutting and black oxide skin, more difficult to remove.
3.6 Scratches caused by human factors are more serious: in the process of lifting, transportation and structural processing, scratches caused by human factors such as bump, drag and hammer are more serious, which makes surface treatment more difficult, but also the main reason for rust after treatment.
3.7 Equipment factors: Scratches and creases caused in the rolling and bending process of profiles and plates are also the main reasons for corrosion after treatment.
3.8 Other factors: stainless steel raw materials in the procurement, storage process, due to lifting, transportation process of bump and scratch is also more serious, is also one of the causes of rust.
4 Preventive measures should be taken
4.1 Storage, hoisting and transportation
4.1.1 Storage of stainless steel parts: there should be a special storage rack. The storage rack should be a wooden or painted surface carbon steel bracket or pad with rubber pad to be isolated from carbon steel and other metal materials. When stored, the storage location should be convenient for lifting, relatively isolated from other material storage areas, and protective measures should be taken to avoid the pollution of dust, oil and rust on stainless steel.
4.1.2 Lifting of stainless steel parts: special lifting tools, such as lifting belts and special clamps, should be used when hoisting. It is strictly prohibited to use wire rope to avoid scratching the surface; And when lifting and placing, should avoid impact bump caused by scratches.
4.1.3 Transportation of stainless steel parts: transportation means (such as car, battery car, etc.) should be used during transportation, and isolation and protective measures should be clean to prevent dust, oil, rust pollution of stainless steel. It is strictly prohibited to drag and avoid bumps and scratches.
4.2 Processing
4.2.1 Processing area: The processing area of stainless steel parts should be relatively fixed. Stainless steel parts processing area of the platform should be taken isolation measures, such as the spread of rubber MATS. Stainless steel parts processing area location management, civilized production should be strengthened to avoid stainless steel parts damage and pollution.
4.2.2 Blanking: The blanking of stainless steel parts adopts shear or plasma cutting, sawing, etc.
Shear: when cutting, it should be isolated from the feeding bracket, and the hopper should also be paved with rubber pads to avoid scratches.
Plasma cutting: After plasma cutting, cutting slag should be cleaned up. Batch cutting, for the completed parts should be cleaned out of the site in time to avoid cutting slag to the workpiece.
(3) Sawing cutting: sawing cutting, clamping should be rubber protection, sawing should clean up the oil on the workpiece, residue and so on.
4.2.3 Machining: stainless steel parts should also pay attention to protection during machining, such as turning and milling, and clean up the oil, iron filings and other debris on the surface of the workpiece after completion of the operation.
4.2.4 Molding processing: in the process of rolling plate and bending, effective measures should be taken to avoid scratches and creases on the surface of stainless steel parts.
4.2.5 Riveting: When the stainless steel parts are paired, forced assembly should be avoided, especially flame roasting calibration assembly. If plasma cutting is temporarily used in the group or production process, isolation measures should be taken to avoid the pollution of other stainless steel parts by cutting slag. After cutting, the slag on the workpiece should be cleaned up.
4.2.6 Welding: The stainless steel parts must be carefully removed before welding oil, rust, dust and other sundries. When welding, argon arc welding should be adopted as far as possible. When manual arc welding is adopted, small current and fast welding should be adopted to avoid swing. It is strictly prohibited to initiate arc in non-welding areas. The ground wire should be properly positioned and firmly connected to avoid arc scratches. Anti-splash measures should be taken during welding (such as brushing white ash, etc.). After welding, stainless steel (not carbon steel) flat shovel should be used to thoroughly clean up slag and spatter.
4.2.7 Multi-layer welding: During multi-layer welding, the slag between layers must be cleaned. Multilayer welding, the temperature between layers should be controlled, generally not more than 60℃.
4.2.8 Weld: The weld joint shall be polished, and there shall be no defects on the surface of the weld, such as slag, porosity, edge biting, spatter, crack, non-fusion, non-penetration, etc. The weld and the base material shall be smooth and smooth, and shall not be lower than the base material.
4.2.9 Orthosis: For the orthosis of stainless steel parts, flame heating method should be avoided, especially repeated heating of the same area is not allowed. When orthopedic, try to use mechanical devices, or use wood hammer (rubber hammer) or cushion rubber cushion hammer, it is prohibited to use hammer hammer, in order to avoid damage to stainless steel parts.
4.2.10 Handling: stainless steel parts in the process of processing for handling, the application of transport tools (such as car, battery car or crane, etc.), and should be clean with isolation and protective measures to prevent dust, oil, rust pollution of stainless steel. Do not drag directly on the platform or ground, and do not knock or scratch.
4.3 Surface Treatment
4.3.1 Cleaning and polishing: If there is any damage, it should be polished, especially the damage caused by scratches and spattering and slag cutting caused by contact with carbon steel parts must be carefully and thoroughly cleaned and polished.
4.3.2 Mechanical polishing: To use appropriate polishing tools for polishing, the treatment should be uniform and consistent, and avoid overthrowing and rescratching.
4.3.3 Oil removal and dust removal: Before pickling and passivation of stainless steel parts, oil pollution, oxide skin, dust and other sundry materials must be removed according to the process.
4.3.4 Water sandblasting treatment: Different microglass beads and different process parameters should be selected according to different treatment requirements, and overspraying should be avoided.
4.3.5 Pickling passivation: The pickling passivation of stainless steel parts must be passivation in strict accordance with the process requirements.
4.3.6 Cleaning and drying: After pickling and passivation, neutralization, washing and drying should be carried out in strict accordance with the process to completely remove the residual acid.
4.3.7 Protection: After the surface treatment of stainless steel parts is completed, it should be well protected to avoid the secondary pollution of personnel touching and oil, dust and other sundry.
4.3.8 Avoid reprocessing: After the surface treatment of stainless steel parts is completed, the reprocessing of the parts or products should be avoided.
Including: chemical tanker, storage tank, pipeline boiler and other stainless steel/mild steel products surface treatment, such as polishing/polishing, pickling/passivation, inspection/supervision, technical consultation, etc.
The main service objects are shipbuilding, petrochemical and food equipment industries.
Plastic surface treatment technology
With the continuous improvement of plastic processing and modification technology, the application field expands rapidly. Different application fields have increasing requirements for plastic surface decoration, material protection, improving bonding and other properties, but the structure and composition of various plastic materials are different, and the corresponding surface properties are also different. Various surface treatment technologies and products adapted to different applications emerge.
Suitable for plastic surface
A variety of treatment techniques have been developed for different needs. Commonly used technologies are: solvent cleaning (degreasing), corona treatment, short-wave ultraviolet radiation treatment, sandpaper treatment, sandblasting treatment, plasma etching, chemical etching, heating treatment, etc. For different materials, often need to choose different treatment methods.
Selection of surface treatment methods
Due to the low surface energy of most plastics, many treatment methods, such as decoration, printing, spraying, etc., can not be directly applicable, and the need for surface treatment first. The adhesion between plastics and various materials is a key problem to be solved in surface treatment. Generally speaking, the bonding property of plastics is related to the material structure and composition.
Structural influence
Polyolefin materials such as PP and PE have very low surface energy, usually only 30-34 dynes. To achieve good bonding, the surface energy is generally required to be not less than 40 dynes. The bonding test shows that the bonding strength of PE can be increased by 10 times after plasma treatment. After chromic acid treatment, the bonding property can be improved by 5 times. After the same treatment, the bond strength of PP increased 200 times after ionization treatment, and 600 times after chromic acid treatment.
Why is the effect of chromic acid on PP so significant but not on PE? This is because each carbon atom in the PP segment has a methyl group (-CH3). Methyl groups are easily oxidized by carboxyl groups after oxygen ionization or chromic acid treatment. Moreover, even if only a few methyl groups are oxidized, the bonding properties and polarity of PP are significantly improved by the presence of carboxyl groups. PE doesn't have this group. It can be seen that the chemical structure of the polymer is an important factor that must be considered in the surface treatment.
Compositional influence
For various blends or copolymers, the material composition will also affect the choice of surface treatment method. Fluoropolymers and their copolymers, for example, have lower surface energies than polyolefins, typically ranging from 18 to 26 dynes. For high fluorine content resins such as PTFE, after sodium naphthenate etching after the bonding performance improved by 10 times, but after oxygen or argon plasma treatment will only improve by 3 times. The trend for PE is the opposite.
However, after plasma treatment or sodium naphthenate treatment, the bonding properties of the copolymer of fluorine resin and PE increased by 10 times. It can be seen that plasma treatment has more interaction with PE, while sodium naphthenate treatment has more interaction with fluorine resin. It can be seen that the treatment properties of different materials can be improved by copolymerization. For copolymers of different components, the corresponding treatment methods should be selected according to the characteristics of the materials.
Selection technique
Different treatment methods have different effects on different polymer structures and components, so the selection of surface treatment methods should also be based on the structure and components of materials. For low surface energy plastics (<35 dynes), the selection is mainly based on experience. And high surface energy plastic, because of its good adhesion, so almost every treatment method is applicable, can be selected according to the convenience of use. In general, the lower the surface energy of the plastic, the more treatment is required. However, some polymers have lower surface energy and can also be bonded directly with solubilizers, such as ABS, PC, PS, AC and PVC. In fact, AC can bond because many acrylic adhesives act as solvents themselves. For those antisolvent materials, such as POM, PPO, PPS, and other polymers containing benzene rings, surface oxidation is usually required for cleaning or grooming. Materials that are more difficult to bond such as polyamines and polyimines often require surface etching to bond.
For polar plastics, such as polyester, epoxy, polyurethane, polyamine, etc., surface treatment methods also have different requirements. In general, the less polarity, the less processing is required. Among these materials, polyester and epoxy have the strongest polarity and need to be bonded on the surface after brushing. Rigid polyurethane is not high polarity, usually with polyurethane adhesive can be bonded, but need to use epoxy surface treatment. Polyamine is one of the least polar and can be bonded without treatment.
For the actual processing process, it is usually necessary to consider the economy of processing, so that it can better meet the needs of actual processing. The various process parameters usually involved, such as processing time, temperature, exposure, drying conditions, etc., need to be carefully considered. When selecting the treatment method, it is necessary to consider the chemical characteristics of the corresponding material, the structure of the polymer chain segment and the special requirements of the application field. High reliability bonding usually requires more surface treatment.
Surface treatment application technology
As manufacturers have higher and higher requirements on product quality, the matching technology and materials to improve the working environment, improve the working efficiency and processing reliability have been developed, and their market applications have been expanded.
Hot molecular bonding processing technology
FTS is a professional manufacturer of pre-treatment equipment for plastic spraying. The company has developed a thermal molecular bonding processing technology (AtmaP) that effectively improves the bonding properties of materials, enhances product quality, and is environmentally friendly. The AtmaP technology is realized by using Cirqual burner. AtmaP processing is mainly to graft a layer of chemical coupling agent on the surface of olefin based plastic parts to improve the bonding property. The combustion flame provided by the Cirqual burner is the only driving force for the coupling agent to spread across the plastic surface. The burners are of lightweight aluminum construction, allowing for quick maintenance and operation, especially for automatic handling. The product is mainly suitable for spraying, bonding, decoration, lamination, printing or need to tape the material surface treatment. According to the report, no other similar process in use today can achieve the effect of AtmaP.
Application of light curing coatings in automotive plastic parts
Engineered plastics or polymer-based composites are already used in many automotive components, which not only require coatings to improve their surface properties, but also sometimes to achieve material performance improvements. The use of plastic instead of glass in car lampshades and mirrors benefits from the treatment of light curing coatings. Polycarbonate has the advantages of easy processing molding, light weight and flexibility is not easy to break, but its surface strength is not enough, not resistant to scratching and scratching and poor weather resistance, easy to yellow. The use of photocurable coatings to improve the surface properties can not only greatly save the coating time but also have good optical friction resistance and meet the requirements of long-term weather resistance. Thanks to new technology, polycarbonate lampshades have now replaced glass almost entirely.
Automotive mirrors are also made of plastic, but must have high reflective performance. To achieve this, the plastic surface must be treated with ultraviolet radiation three times. First of all, the plastic surface through ultraviolet irradiation to produce photochemical reaction to increase the surface tension, to facilitate the light curing coating leveling and adhesion; After curing with a coated light curing varnish, the plastic surface becomes flat and prone to metallization
Key words:联合国,志源电池厂
Related information
2022-04-06
National hotline:0086-0752-2606595
Contact person:Business Ningqianghui
Mobile phone:13923626229
Mailbox:sales@cheefat.com
Address:Building # 409/404,Longxi Plating Park,Longxi Town, Boluo County, Huizhou City, Guangdong Province, 516121, China.
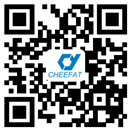
Copyright © 2022 CheeYuen Surface Treatment(Huizhou)Co.,Ltd. All Rights Reserved 粤ICP备2021109730号 Powered by www.300.cn SEO