Common 10 kinds of surface treatment methods, you know how many?
Release time:
2012-01-07
Source:
Xinmin.com
Surface treatment is the process of artificially forming a layer on the surface of the matrix material which is different from the mechanical, physical and chemical properties of the matrix. The purpose of surface treatment is to meet the corrosion resistance, wear resistance, decoration or other special functional requirements of the product.
Here are 10 common surface treatments:
01 Polishing
Polishing refers to the processing method using mechanical, chemical or electrochemical action to reduce the surface roughness of the workpiece so as to obtain a bright and smooth surface. It is the modification processing on the surface of the workpiece by using polishing tools and abrasive particles or other polishing media.
Polishing does not improve dimensional accuracy or geometric accuracy of the workpiece, but is done to obtain a smooth surface or mirror finish, and sometimes to remove gloss (extinction).
Usually polishing wheel as polishing tool. The polishing wheel is generally made of multiple layers of canvas, felt or leather, and is clamped on both sides with round metal plates. The rim of the wheel is coated with polishing agent which is evenly mixed by micro-powder abrasive and grease.
During polishing, the high-speed rotating polishing wheel (the circumference speed is more than 20 m/s) is pressed to the workpiece, so that the abrasive produces rolling and micro cutting on the workpiece surface, so as to obtain a bright machining surface, the surface roughness is generally up to Ra0.63 ~ 0.01 micron. When using non-greasy matting polish, the glossy surface can be matted to improve appearance.
For different polishing processes: rough polishing (basic polishing process), medium polishing (finishing process) and fine polishing (polishing process), the selection of suitable polishing wheel can achieve the best polishing effect, and improve the polishing efficiency.
02 Sand Blasting
The process of cleaning and coarsening the substrate surface by the impact of high speed sand flow.
The compressed air is used as the power to form a high-speed jet beam jet material (copper ore, quartz sand, emery, iron sand, Hainan sand) high-speed jet to the surface of the workpiece need to be treated, so that the surface of the workpiece surface appearance or shape changes.
Due to the impact of abrasive on the workpiece surface and cutting effect, so that the workpiece surface to obtain a certain degree of cleanliness and different roughness, so that the workpiece surface mechanical properties are improved, so improve the workpiece fatigue resistance, increase the adhesion between it and the coating, prolong the durability of the coating film, but also conducive to the flow of paint and decoration.
03 Drawing
Surface drawing treatment is a surface treatment means to form lines on the workpiece surface through grinding products and play a decorative effect. According to the different lines after drawing can be divided into: straight drawing, random drawing, ripple, spiral.
Because surface wire-drawing can reflect the texture of metal materials, it has been more and more popular and widely used by more and more users.
04 Anodizing
An electrolytic oxidation process in which the surface of aluminum and aluminum alloys is usually transformed into an oxide film that has protective, decorative, and some other functional properties.
The anodizing of aluminum from this definition only includes the forming of anodized film. An oxide film is formed on the surface of a metal or alloy as an anode by electrolysis. Metal oxide film changes the surface state and performance, such as surface coloring, improve corrosion resistance, enhance wear resistance and hardness, protect the metal surface, etc.
Aluminum and its alloy are placed in the corresponding electrolyte (such as sulfuric acid, chromic acid, oxalic acid, etc.) as the anode, under specific conditions and external current, electrolysis is carried out. Anodic aluminum or its alloy oxidized, forming a thin layer of alumina on the surface, its thickness is 5 ~ 30 microns, hard anodic oxide film up to 25 ~ 150 microns.
Anodized aluminum or its alloy, improve its hardness and wear resistance, up to 250 ~ 500 kg/square mm, good heat resistance, hard anodized film melting point up to 2320K, excellent insulation, breakdown voltage up to 2000V, enhance the corrosion resistance, In ω=0.03NaCl salt spray after several thousand hours without corrosion.
The thin layer of oxide film has a large number of micro holes, can absorb various lubricants, suitable for the manufacture of engine cylinder or other wear-resistant parts; The membrane has strong adsorption capacity and can be colored into a variety of beautiful and gorgeous colors.
Non-ferrous metals or their alloys (such as aluminum, magnesium and their alloys, etc.) can be anodized. This method is widely used in machinery parts, aircraft and automobile parts, precision instruments and radio equipment, daily necessities and architectural decoration.
Generally speaking, the anode is made of aluminum or aluminum alloy as the anode, the cathode is selected lead plate, aluminum and lead plate together in aqueous solution, which contains sulfuric acid, oxalic acid, chromic acid, etc., for electrolysis, so that the surface of the aluminum and lead plate forms an oxide film. Among these acids, the most widespread is anodizing with sulfuric acid.
【 Technological process 】
Monochrome, gradient:
Polishing/sandblasting/drawing → oil removal → anodizing → neutralization → dyeing → hole sealing → drying
Two-color:
① Polishing/sandblasting/drawing → oil removal → shielding → anodizing 1→ anodizing 2 → hole sealing → drying
② Polishing/sandblasting/drawing → oil removal → anodizing 1 → radium carving → anodizing 2 → hole sealing → drying
【 Technical characteristics 】
1. Enhance strength
2. Realize any color except white
3, the realization of nickel free sealing hole, to meet the requirements of Europe, the United States and other countries on nickel free.
05 Electrophoresis
The process is divided into anode electrophoresis and cathode electrophoresis. If the coating particles are negatively charged and the workpiece is an anode, the coating particles are deposited into a film on the workpiece under the action of electric field force, which is called anode electrophoresis; On the other hand, if the coating particles are positively charged, the workpiece is the cathode, and the coating particles are deposited on the workpiece into a film called cathode electrophoresis.
Pretreatment of workpiece (oil removal → hot water washing → rust removal → cold water washing → phosphating → hot water washing → passivation) → anodic electrophoresis → post-treatment of workpiece (clean washing → drying).
1, oil removal: the solution is generally hot alkaline chemical oil removal liquid, the temperature is 60℃ (steam heating), the time is about 20min.
2. Hot water washing: temperature 60℃ (steam heating), time 2min.
3, rust removal: with H2SO4 or HCl, such as with hydrochloric acid rust removal liquid, HCl total acidity ≥43 points; Free acidity >41 points; Plus cleaning agent 1.5%; Wash at room temperature for 10 ~ 20min.
4, cold water washing: flow in cold water for 1min.
5, phosphating: with medium temperature phosphating (60℃ phosphating 10min), phosphating liquid available commercially finished products.
The above process can also be replaced by sandblasting → washing.
6, passivation: with phosphating liquid supporting drugs (provided by the manufacturer selling phosphating liquid), 1 ~ 2min at room temperature.
7, anode electrophoresis: electrolyte composition is H08-1 black electrophoresis paint, solid mass fraction of 9% ~ 12%, distilled water mass fraction of 88% ~ 91%. The voltage is (70±10) V; The time is 2 ~ 2.5min; The paint temperature is 15 ~ 35℃. The PH value of the paint is about 8 ~ 8.5. Note that the workpiece inlet and outlet slot should be powered off. During electrophoresis, the current decreases gradually with the thickening of the paint film.
8. Clean water: wash in running cold water.
9, drying: in the oven at (165±5) ℃ temperature 40 ~ 60min can be baked.
06 PVD
Physical Vapor Deposition (physical vapor deposition) refers to the technology of arc discharge with low voltage and high current under vacuum condition to vaporize the target material and ionize both the vaporized substance and gas by gas discharge, and the vaporized substance and its reaction products are deposited on the workpiece by the acceleration of electric field.
Physical vapor deposition technology has the advantages of simple process, environmental improvement, no pollution, less consumables, uniform and dense film formation, and strong binding force with matrix.
The technology is widely used in aerospace, electronics, optics, machinery, construction, light industry, metallurgy, materials and other fields, can prepare wear-resistant, corrosion-resistant ornaments, decoration, conductive, insulating, photoconductive, piezoelectric, magnetic, lubricating, superconducting and other properties of the film layer.
07 plating
Is the use of electrolytic effect of metal or other materials to attach a layer of metal film on the surface of the process so as to prevent metal oxidation (such as corrosion), improve wear resistance, electrical conductivity, reflective, corrosion resistance (copper sulfate, etc.) and improve the appearance of the role. The outer layer of many coins is also electroplated.
08 Etching
Usually referred to etching, also known as photochemical etching, refers to the removal of the protective film of the etched area through exposure platemaking and development, and contact with chemical solution during etching to achieve the effect of dissolution corrosion and the formation of concave and convex or hollow forming effect.
Exposure method: engineering according to the figure out the size of the material preparation - material cleaning - drying → film or coating → drying → exposure → development → drying - etching → film removal →OK
Screen printing method: opening → cleaning plate (stainless steel and other metal materials)→ screen printing → etching → film removal →OK
09 Spraying
Spraying A coating method in which droplets are dispersed into uniform and fine droplets on the surface of the coated object by means of a spray gun or a dish atomizer with the help of pressure or centrifugal force. It can be divided into air spraying, airless spraying, electrostatic spraying and the derivations of the above basic spraying forms, such as large flow and low pressure atomizing spraying, thermal spraying, automatic spraying, multi-group spraying and so on.
Spraying operation has high production efficiency and is suitable for manual operation and industrial automatic production. It is widely used in hardware, plastics, furniture, military industry, ships and other fields. It is one of the most widely used painting methods nowadays.
Spraying operation needs environment requirements of one million to one hundred level of dust-free workshop, spraying equipment includes spray gun, spray painting room, paint room, curing furnace/drying furnace, spraying workpiece conveying equipment, fog elimination and waste water, waste gas treatment equipment, etc.
Large flow and low pressure atomizing spraying is characterized by low atomizing pressure and low air jet velocity. Low atomizing coating running speed improves the situation that the coating bounces off the surface of the coated material. The paint rate from the ordinary air spraying 30% ~ 40%, increased to 65% ~ 85%. Apply the finish to the surface of the leather with an airbrush or a spray gun in light leather finishing.
10 radium carving
Also called laser engraving or laser marking, is a surface treatment process using optical principles. The high intensity focusing laser beam emitted by the laser is used at the focal point to oxidize the material and thus process it.
Marking effect is to reveal the deep material through the evaporation of the surface material, or to cause the chemical and physical changes of the surface material through the light energy, or to burn off part of the material to "carve" the trace, showing the graphics and words that need to be etched.
Key words:联合国,志源电池厂
Related information
2022-04-06
National hotline:0086-0752-2606595
Contact person:Business Ningqianghui
Mobile phone:13923626229
Mailbox:sales@cheefat.com
Address:Building # 409/404,Longxi Plating Park,Longxi Town, Boluo County, Huizhou City, Guangdong Province, 516121, China.
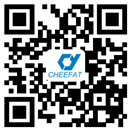
Copyright © 2022 CheeYuen Surface Treatment(Huizhou)Co.,Ltd. All Rights Reserved 粤ICP备2021109730号 Powered by www.300.cn SEO